Riccoplast: Innovating Plastic Production with My AR Studio
Riccoplast, a leading company in plastic manufacturing, has integrated My AR Studio into its operations, enhancing the way they communicate with clients and optimizing their production processes, maintaining the excellence that has always defined them.
Founded over 50 years ago, Riccoplast is a well-established company in the plastic manufacturing industry. Based in Italy, the company has distinguished itself through its ability to innovate and the superior quality of its products, serving a wide range of industries from automotive to packaging. Their expertise in plastic transformation has made them a reliable partner for numerous leading companies in their respective sectors.
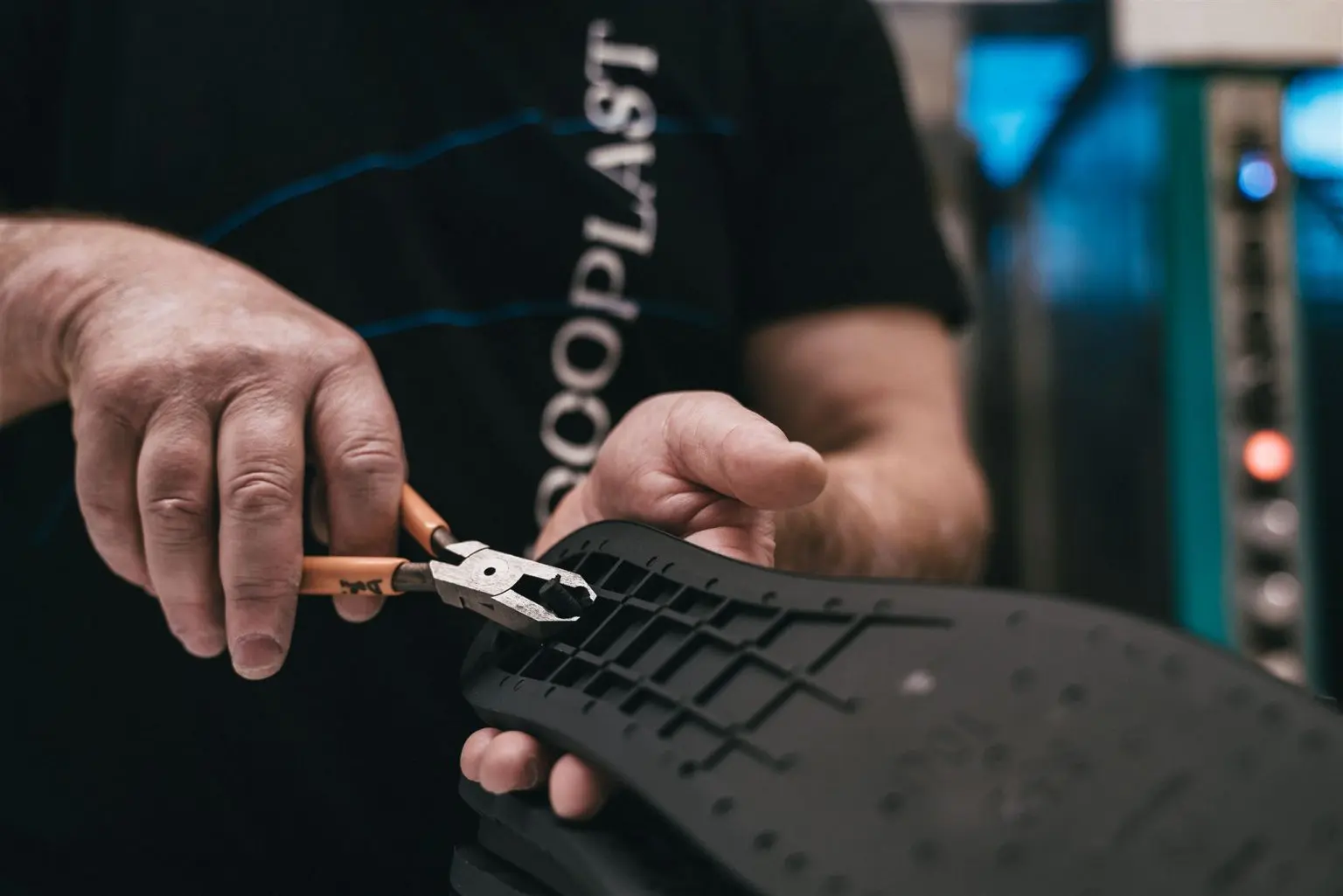
Project summary
The design team at Riccoplast, tasked with improving how they present their complex plastic products to clients, sought a solution that could elevate the clarity and interactivity of their product showcases. By integrating advanced 3D models and augmented reality through My AR Studio, Riccoplast found an innovative way to revolutionize client communication and enhance the understanding of their technical solutions, setting a new standard in product presentation within the plastic manufacturing industry.
The Team
The Riccoplast team is composed of highly skilled professionals dedicated to ensuring the highest quality at every stage of the production process. Through continuous investment in training and technology, the team is equipped to tackle the most complex challenges and meet the specific needs of clients, consistently upholding a high standard of excellence.
Paolo Tronchetti
Paolo Tronchetti leads Riccoplast from the perspective of design and CAD engineering. With a deep understanding of the plastic industry and a strong focus on innovation, Paolo plays a crucial role in developing the company's strategies and implementing new technologies. Under his guidance, Riccoplast has continued to push the boundaries of what is possible in design and manufacturing, integrating advanced technological solutions to enhance both production and client communication.
The Challenge
Riccoplast faced the challenge of improving the presentation of their products and processes to clients. The goal was to find a solution that would allow them to showcase the technical and functional characteristics of their plastic products in a detailed and interactive way, overcoming the limitations of traditional presentations and helping clients better understand the potential of their solutions.
The Solution
With My AR Studio, Riccoplast has revolutionized the way they present their products to clients. Using augmented reality, the company can now create detailed 3D models of their plastic products that clients can view and interact with in their real-world environments. This technology allows clients to closely examine the product details, visualizing technical aspects and better understanding how Riccoplast’s solutions can be integrated into their own production processes.
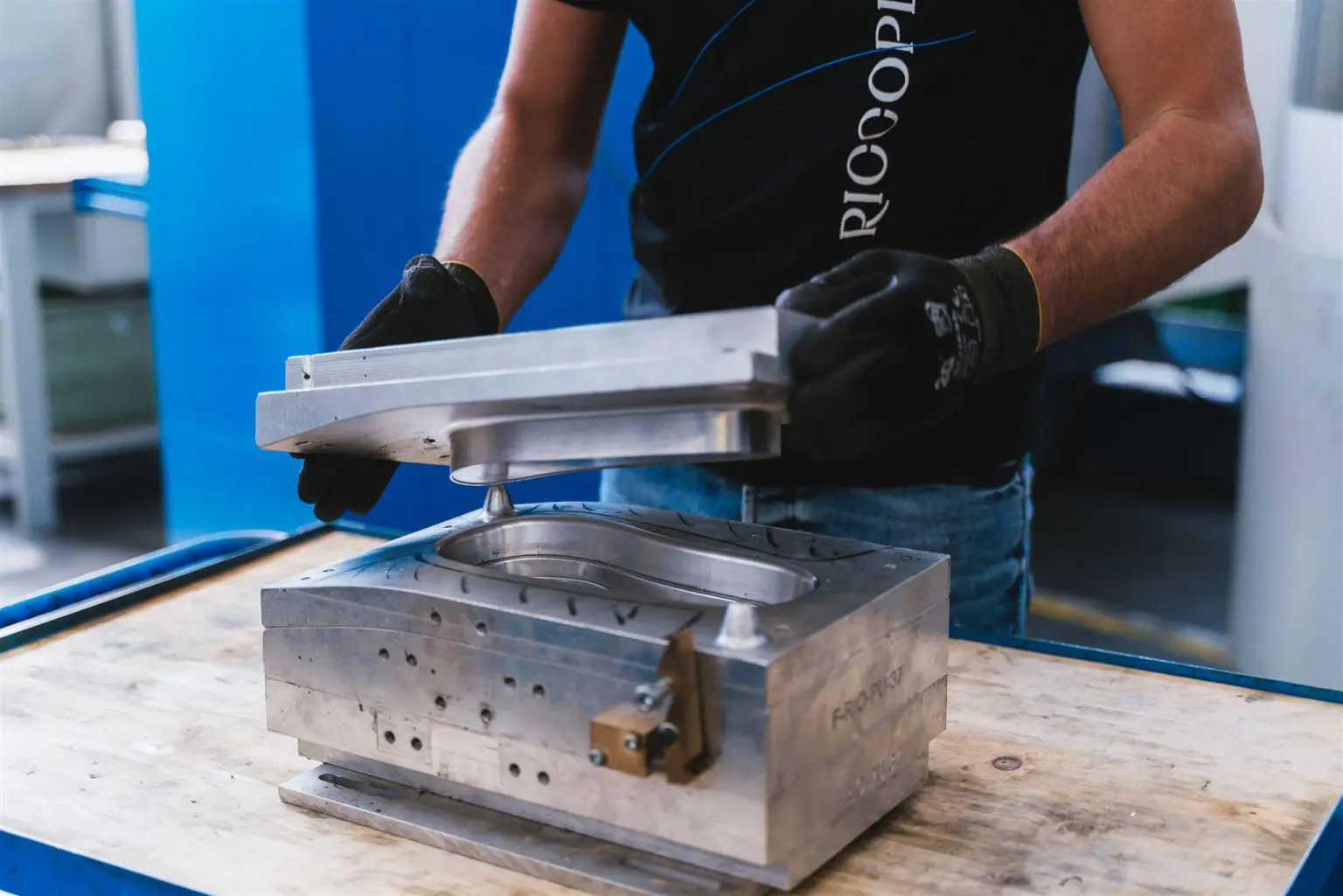
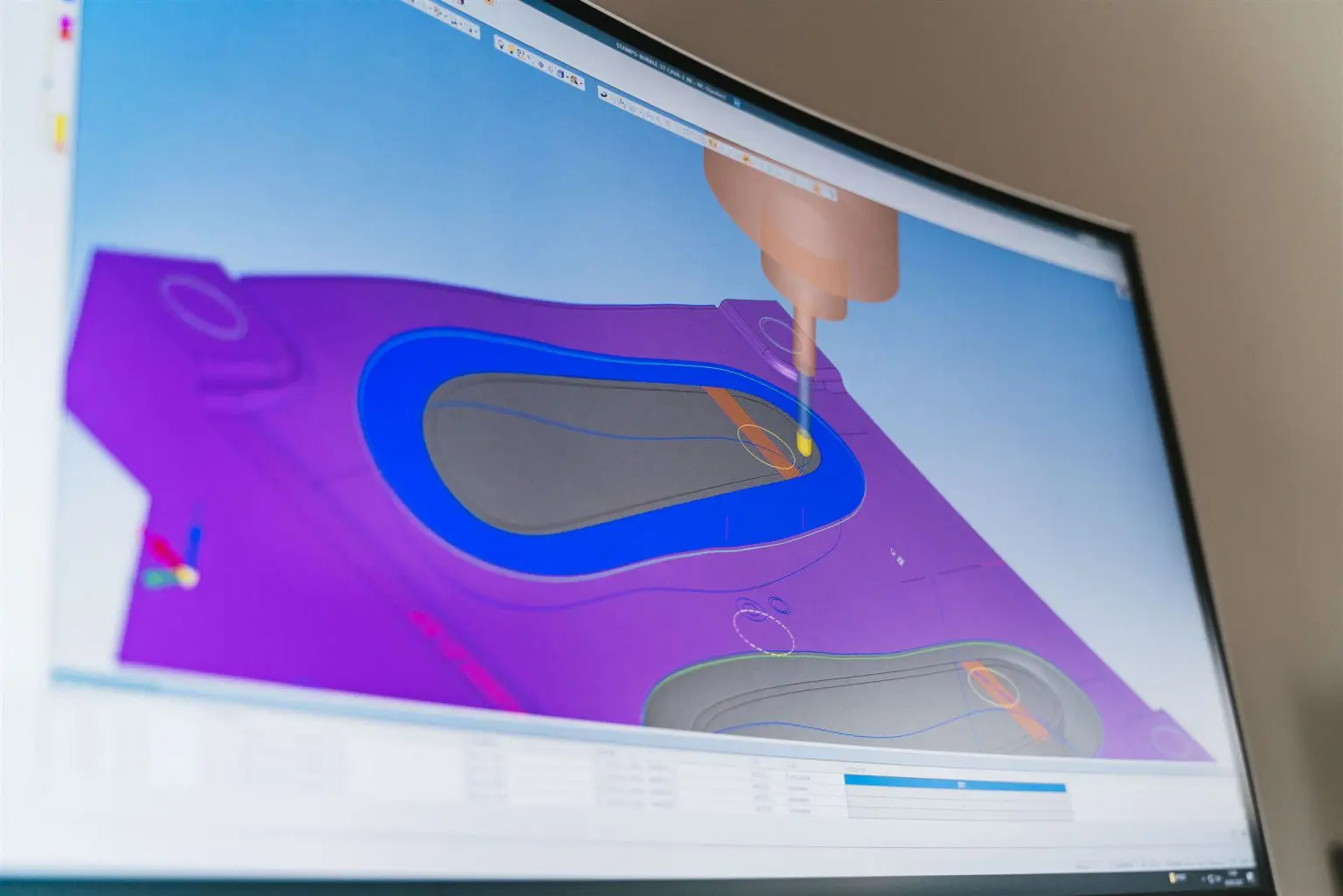
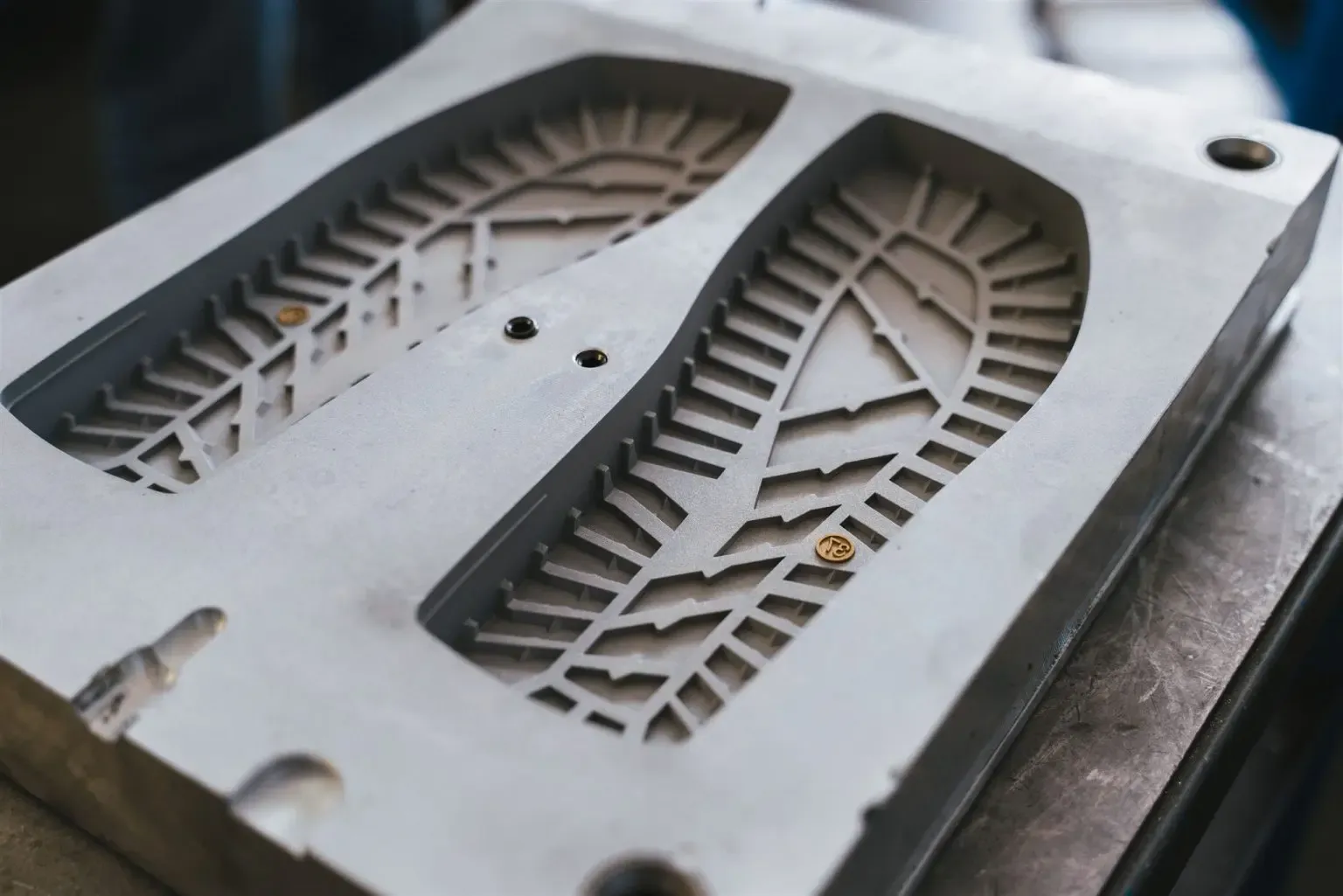
Mold design and prototyping at Riccoplast.
A Significant Step in the Process
One key challenge we encountered was managing model complexity. Our designs typically involve creating the sole using CAD software, which often includes attaching it to an upper scanned through photogrammetry. The rubber texture on the sole, generated by an algorithm, is highly detailed and consists of millions of polygons. Similarly, photogrammetry produces point clouds with equally dense polygon counts.
To present these models to our clients over the Internet in a fast and efficient manner, we needed to significantly reduce the size of the models by several orders of magnitude.
With the support of the My AR Studio team, we developed a workflow and implemented new techniques to compress this high-fidelity data into a format that could run smoothly on a smartphone. We employed two main techniques to achieve this. First, we created a low-poly version of the sole and then baked the high-poly model details into a texture applied to the low-poly model. This process allowed the intricate rubber pattern to be represented by a normal map and an occlusion map. For the photogrammetry model, we applied decimation and smoothing techniques, which proved effective for the dense, organic meshes we work with, making retopology unnecessary at this stage.
The following graphs illustrate the reduction in the number of polygons and vertices before and after optimization. We managed to scale down from millions of polygons to tens of thousands for a fast and deliverable AR experience.
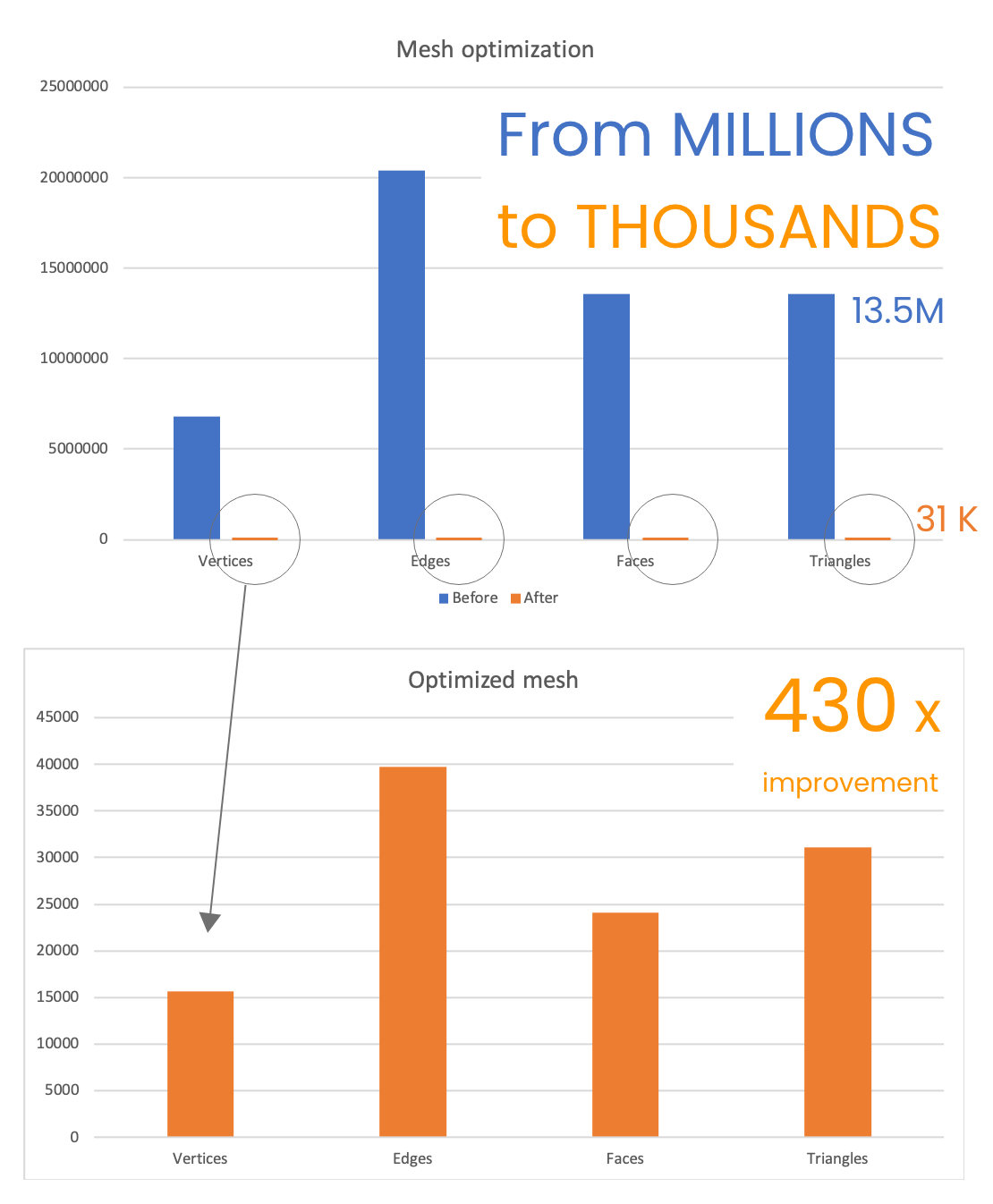
The following screenshots show the original high-poly model, the optimized low-poly models, and the final low-poly model with baked normal and ambient occlusion textures applied.
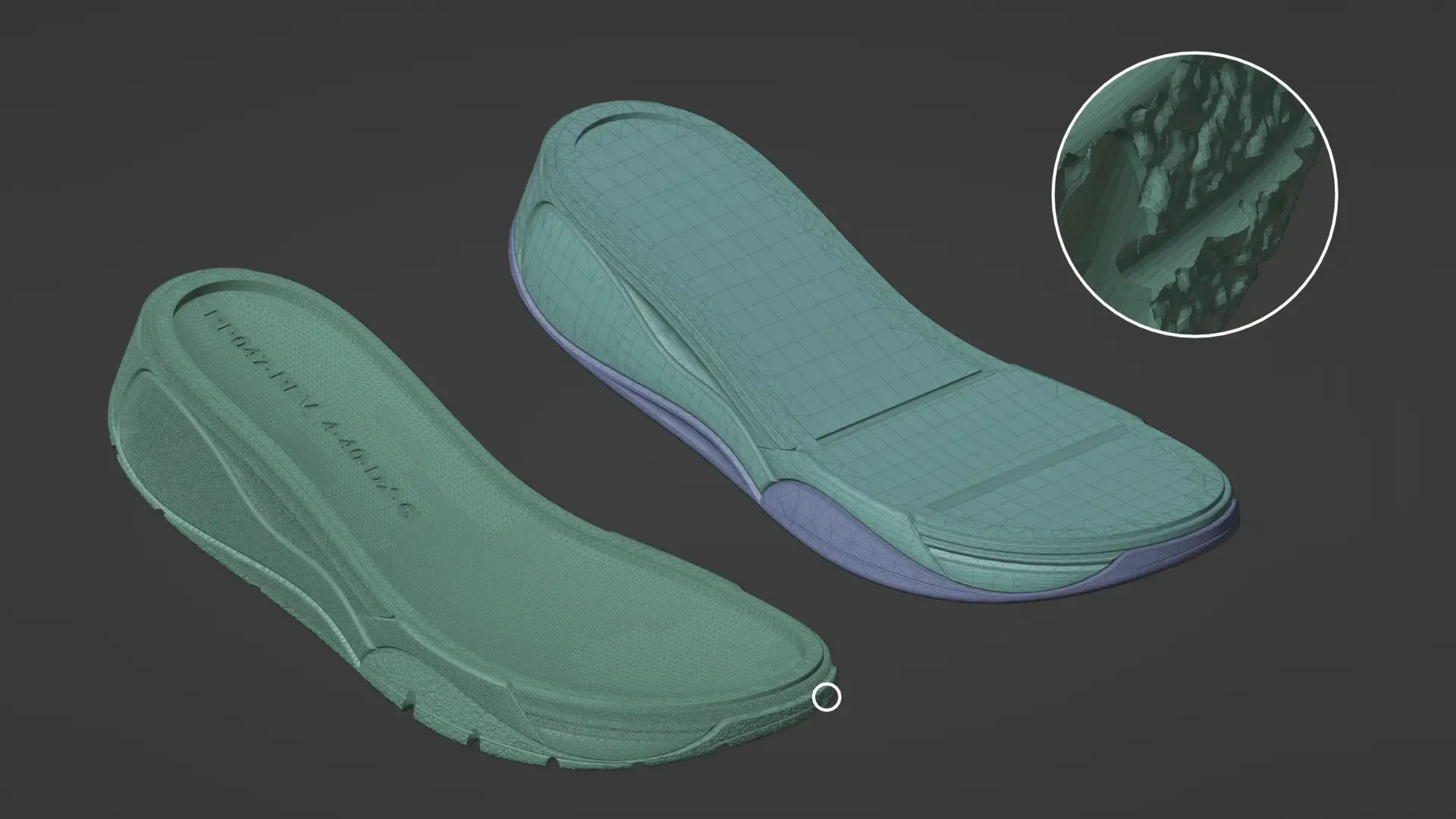
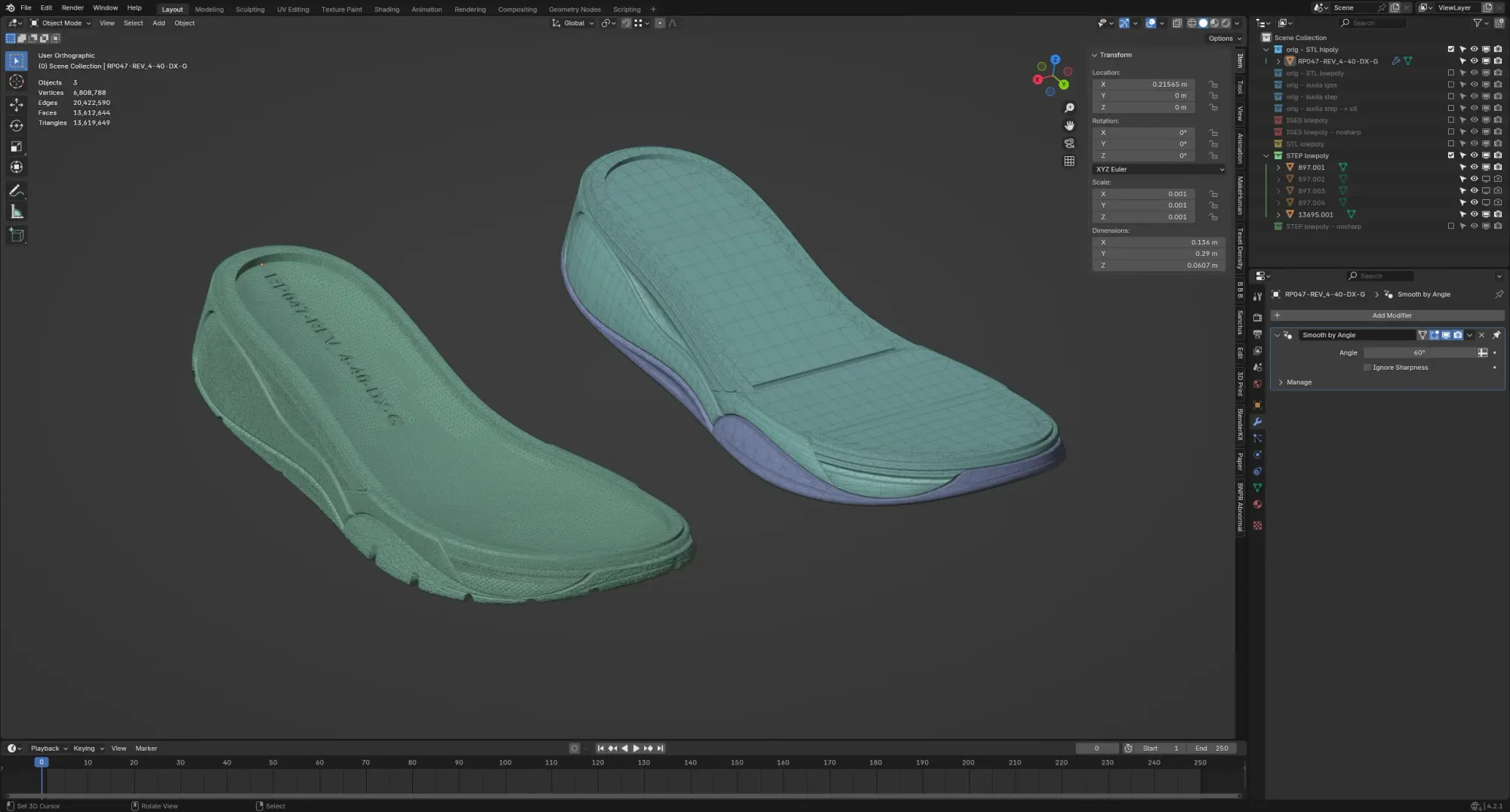
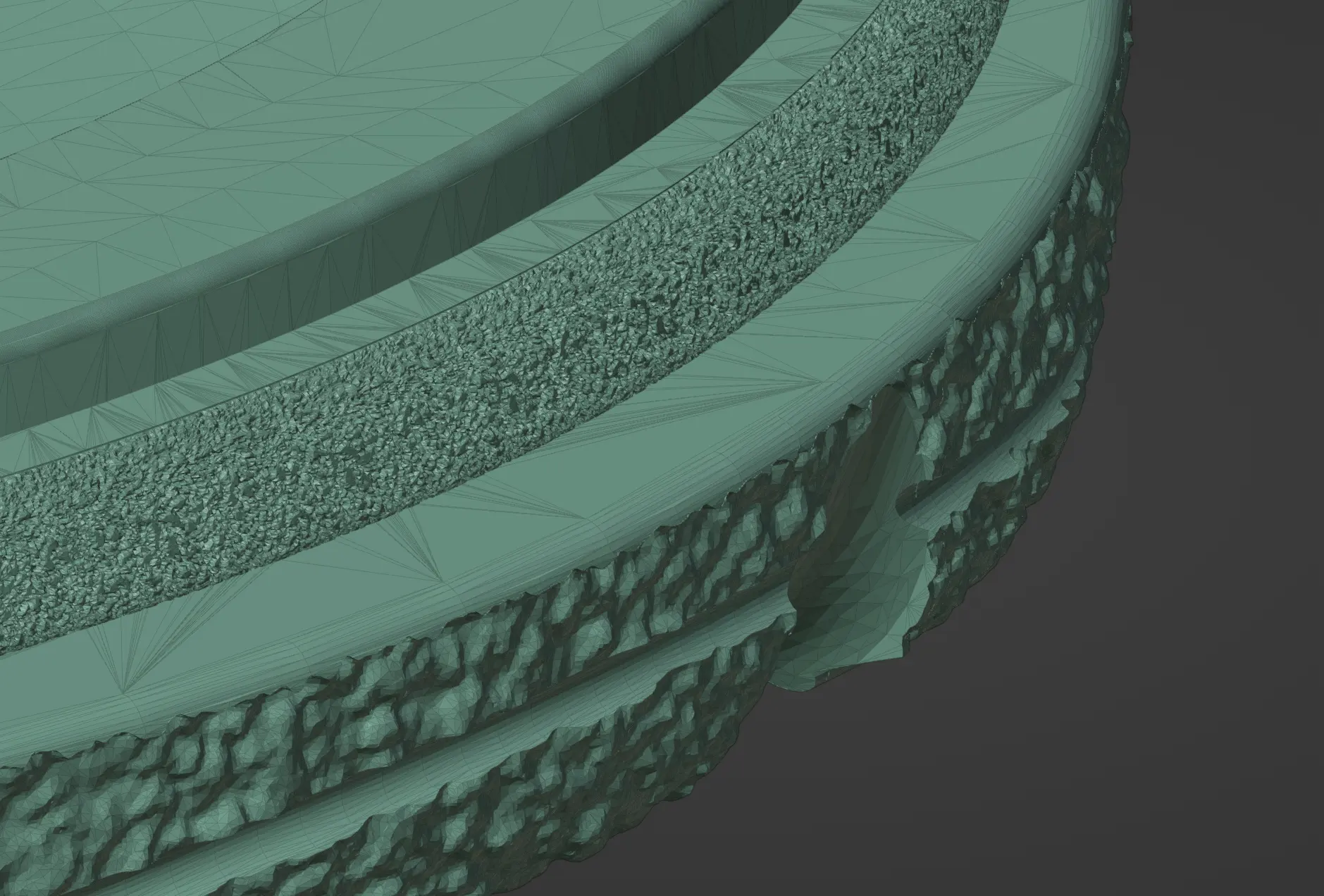
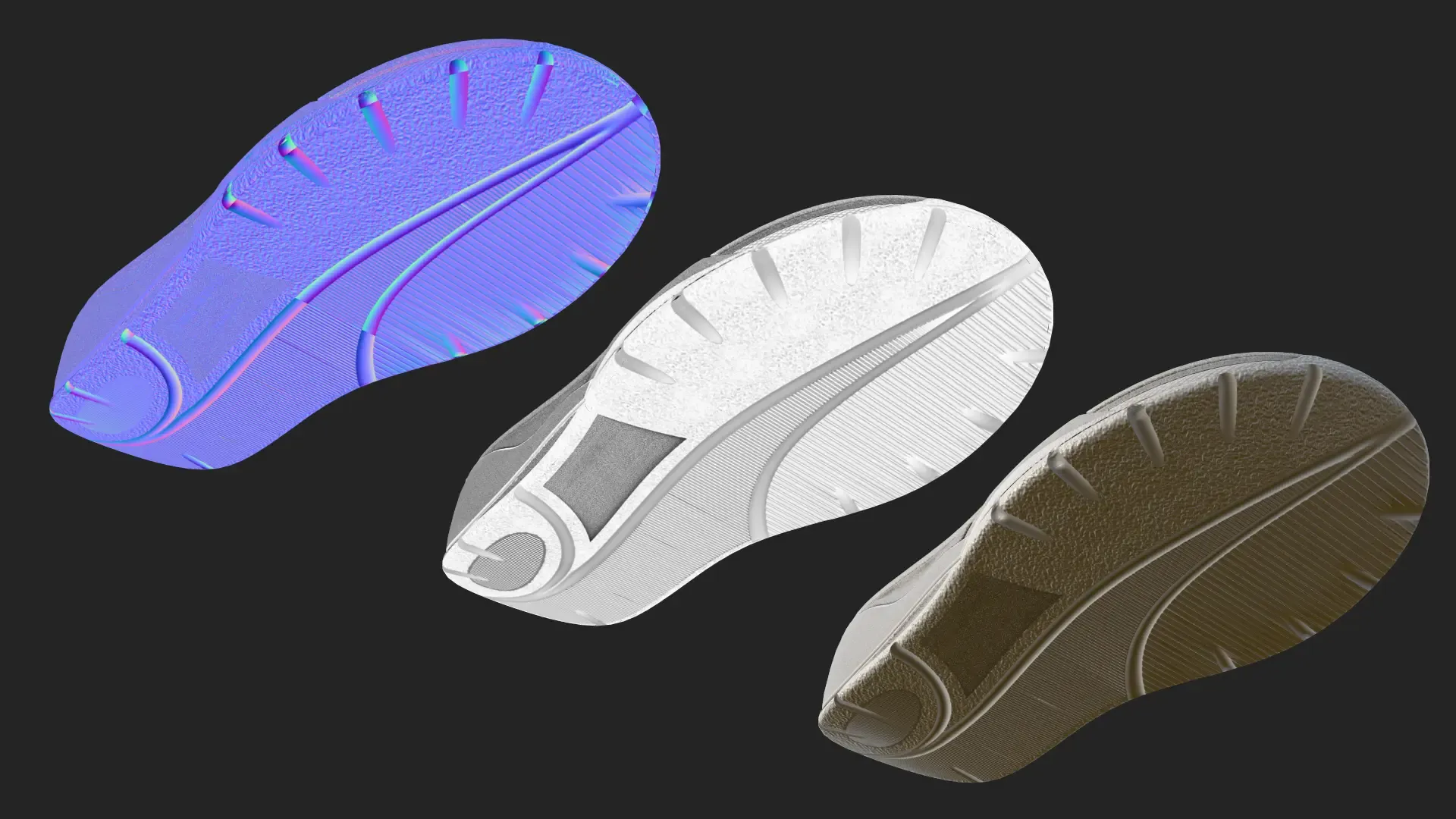
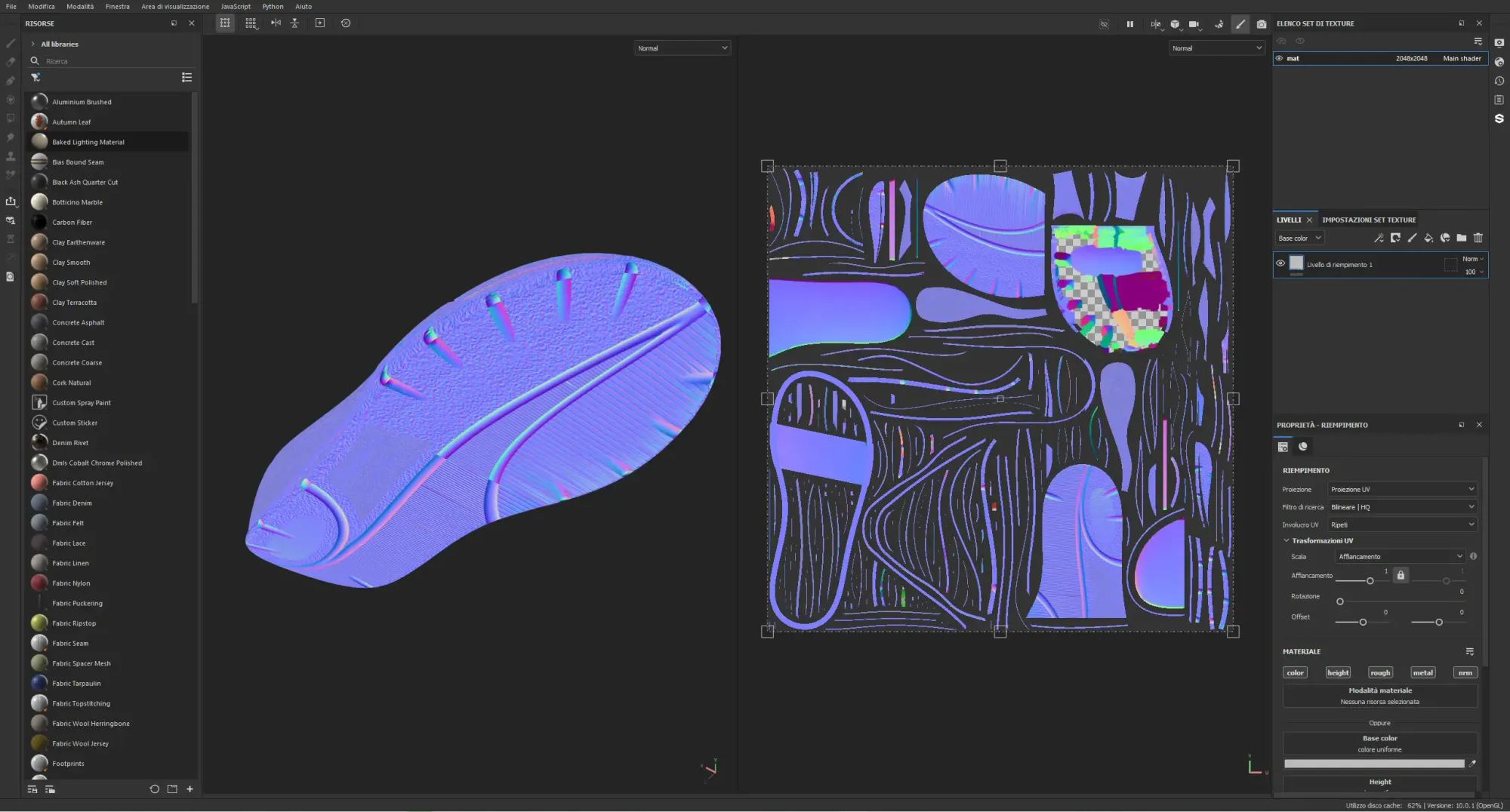
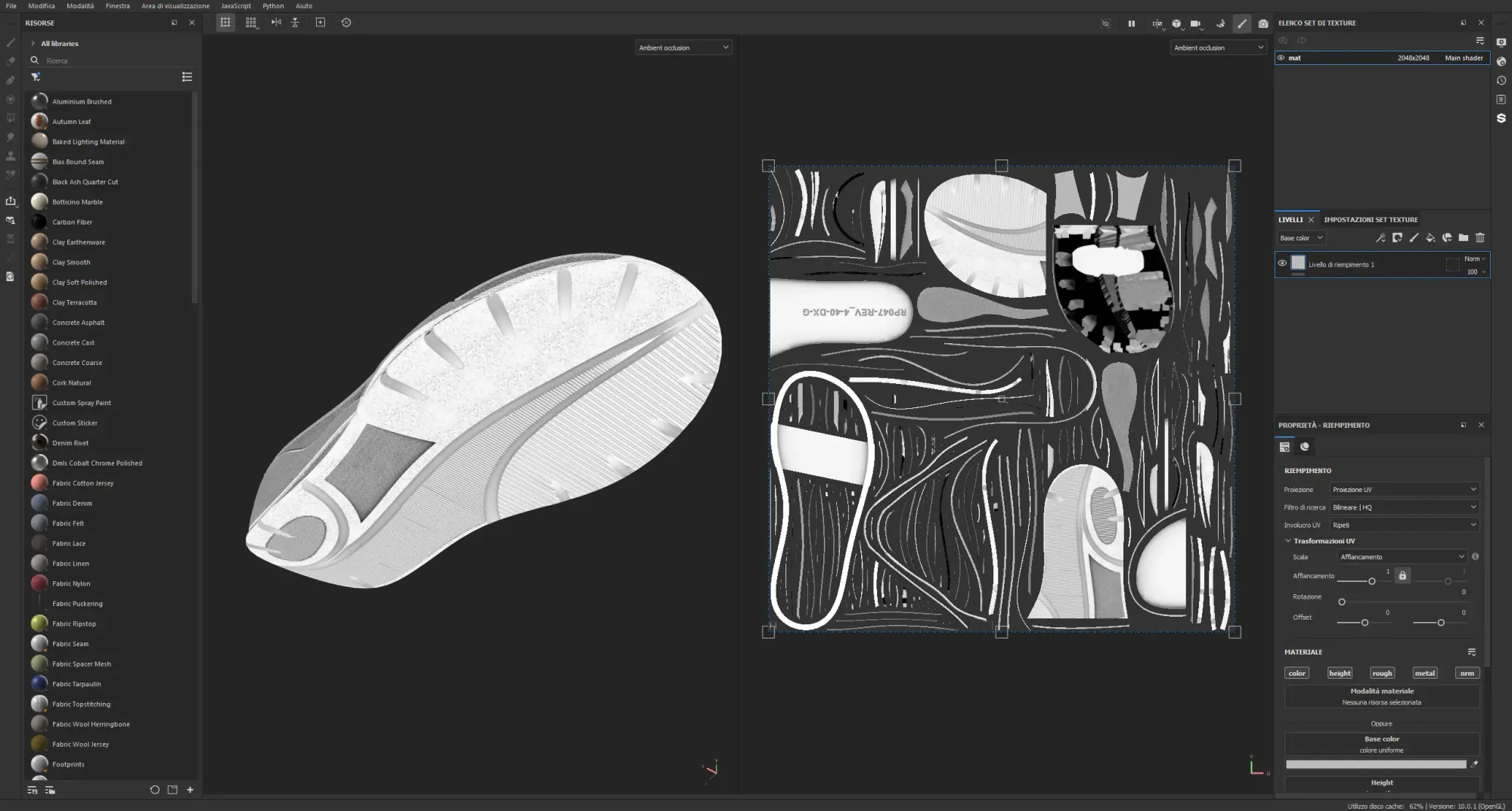
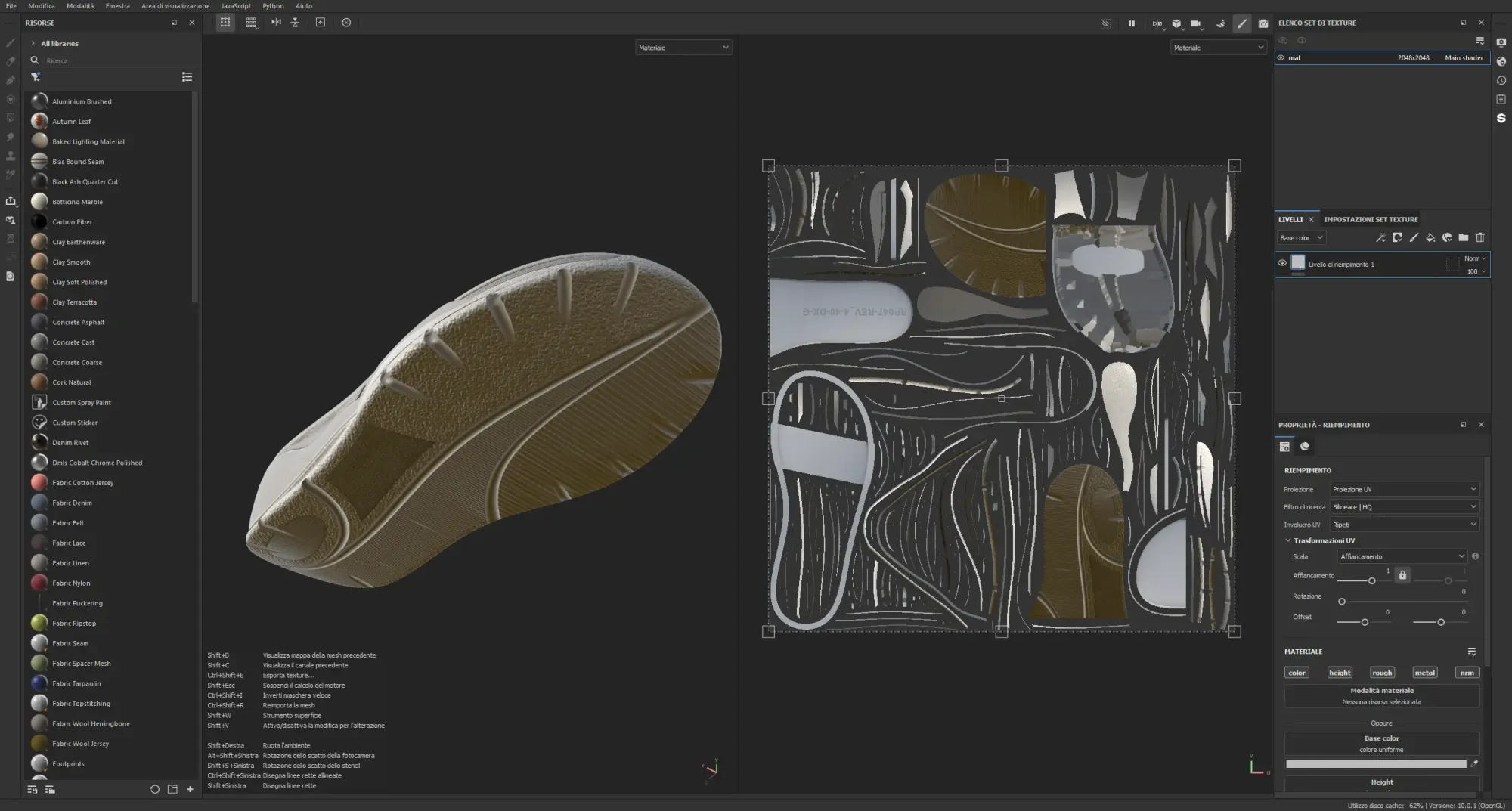
The optimization process involved the creation of a low poly version and the baking of the normal and occlusion maps from the high poly model.
Looking Forward
Riccoplast plans to further expand its use of My AR Studio, exploring more advanced applications to optimize both production and product customization. Paolo Tronchetti and his team are considering developing online configurators that would allow clients to customize products and view their configurations in augmented reality, directly within their environments. This innovation could significantly enhance the client experience, making the product selection and customization process more interactive and immediate.
Our Experience
“Our experience with My AR Studio has been extremely positive,” says Paolo Tronchetti, design and CAD engineering lead at Riccoplast. “The platform has enabled us to elevate our products to a new level, making them not only visually appealing but also incredibly realistic. For a company like ours, where precision and quality are essential, the ability to showcase our products in this way has been a real game-changer. We are excited to continue exploring the potential of this technology to further improve our approach.”